In a world where environmental consciousness is gaining momentum, the concept of zero waste manufacturing has emerged as a beacon of hope for sustainable production practices. The need for innovative approaches to manufacturing has never been more pressing. Here we will delve into the concept of zero waste manufacturing, exploring its principles, benefits, challenges, and the potential it holds for a more sustainable future.
What is Zero Waste Manufacturing?
Zero waste manufacturing is a holistic approach to production that aims to minimize waste generation at every stage of the manufacturing process. Though it is technically impossible to eliminate all waste in the manufacturing process, the core idea is to design and implement systems that prevent or divert waste from landfills, incineration, or the environment. This involves rethinking traditional manufacturing methods and embracing innovative techniques that prioritize resource efficiency and environmental responsibility.
Design for Sustainability:
Zero waste manufacturing begins from the bottom up with product design. Designers are encouraged to create products with a lifecycle approach, considering the environmental impact at every stage, from raw material extraction to disposal. Designing for durability, reparability, and recyclability ensures that products have a longer life cycle and generate less waste. Choosing materials that are less harmful to the environment are a crucial component of zero waste manufacturing.
Circular Economy Practices:
Embracing a circular economy involves keeping resources in use for as long as possible. This includes recycling materials, refurbishing products, and reusing components. By closing the loop and minimizing the extraction of new resources, zero waste manufacturing contributes to a more sustainable and regenerative economic model. The fewer times you have to replace a product, it will generally have a smaller impact on the environment.
Lean Manufacturing:
Lean manufacturing principles focus on reducing inefficiencies, eliminating waste, and optimizing production processes. By streamlining operations, manufacturers can minimize resource use and energy consumption, ultimately contributing to a more sustainable and cost-effective production system. Efficient manufacturing means less scrapped parts, ultimately reducing waste and improving costs.
Benefits of Zero Waste Manufacturing:Environmental Conservation:
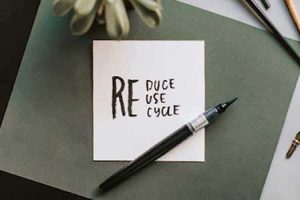
The most obvious benefit of zero waste manufacturing is its positive impact on the environment. By reducing the amount of waste sent to landfills or incinerators, this approach helps conserve natural resources, minimize pollution, and decrease greenhouse gas emissions.
Cost Savings:
While transitioning to zero waste manufacturing may require an initial investment in new technologies and processes, the long-term benefits often translate into significant cost savings. Reduced waste disposal costs, energy savings, and increased operational efficiency contribute to a more financially sustainable business model.
Finding Zero Waste Manufacturers
Environmental Conservation:
The most obvious benefit of zero waste manufacturing is its positive impact on the environment. By reducing the amount of waste sent to landfills or incinerators, this approach helps conserve natural resources, minimize pollution, and decrease greenhouse gas emissions.
Cost Savings:
While transitioning to zero waste manufacturing may require an initial investment in new technologies and processes, the long-term benefits often translate into significant cost savings. Reduced waste disposal costs, energy savings, and increased operational efficiency contribute to a more financially sustainable business model.
At Global Trade Specialists, we take care to make sure our manufacturers implement as many of these strategies as possible to help reduce waste and improve the cost for you.
Zero waste manufacturing is not just a lofty goal but a necessary evolution in the world of production. As we navigate the challenges of an ever changing world, adopting sustainable manufacturing practices becomes imperative. By embracing the principles of zero waste manufacturing, businesses can contribute to a healthier planet, create resilient economies, and build a legacy of responsible production for future generations.